🤖 AI-Generated Content
This content has been created using artificial intelligence. While we strive for accuracy, please verify important information independently.
A conversation has been going around for some time, nearly thirteen years now, about knives and the people who make them. It seems a lot of folks are still talking about an older post, so, it feels like the right moment to clear things up a bit. This piece comes directly from Joshua Jacobs, who wants to share his side of the story, as he is the son of Jason Jacobs, a name some of you might know from the knife-making community.
You see, there's been some talk about how the Jacobs family handles their knife business. Joshua wants everyone to know that, yes, they do make knives. He can, and will, back that up. This isn't just about selling a product; it’s about a family connection to the craft, even if the methods have been, well, a topic of discussion for a while. It's about bringing clarity to a long-standing conversation, which is, you know, pretty important for everyone involved.
This discussion also touches on the economics of knives, especially custom ones, and what makes them worth what they are. It also brings up the personal side of things, like trying to get an old, much-loved knife fixed up. So, this article is here to shed some light on these topics, offering a more personal perspective on the knife world, from the people who live and breathe it, and perhaps, just a little, to address some of those lingering questions.
- Abby Berner Fanfix Leaked
- Jameliz Benitez Leaked
- Iggy Azalea Onlyfans Leaks
- Somali Telegram Link
- Misty Loman Who Is She
Table of Contents
- Joshua Jacobs - A Look at the Family Knife Legacy
- The Craft of Knifemaking - What's Really Going On?
- Understanding Value - Beyond the Initial Purchase
- Finding the Right Hands - Repairing a Piece of History
Joshua Jacobs - A Look at the Family Knife Legacy
Joshua Jacobs has stepped forward to talk about his family's connection to the knife business. He is the son of Jason Jacobs, a name that, for some, is very familiar in discussions about knives. This connection means Joshua has grown up around the craft, seeing how things work from the inside, so to speak. He's speaking up because an old online post from over a decade ago keeps popping up, creating confusion or maybe just keeping a certain idea alive about their operations. He feels it's important to set the record straight, which, you know, makes a lot of sense when your family's name is part of the conversation.
It seems that the Jacobs family has been involved in the knife trade for quite some time. Joshua himself confirms that they do, indeed, make knives. This isn't just a casual statement; he says he can, and will, verify this fact. This kind of directness is pretty helpful when there are lingering questions about a business, especially one that has been around for a while. It shows a willingness to be open, which is, really, a good thing for anyone looking for information.
The discussion around the Jacobs' knife business has, as a matter of fact, included talk about how they might have acquired some knives, possibly inexpensive ones, given them a new stamp, and then sold them again. This practice, often called "re-stamping," has been a point of contention for a long time, apparently. Joshua's statement seems to be a way of addressing these long-standing ideas, bringing his own voice to a story that has been circulating for years. It’s a way of saying, "Here's who I am, and here's what I know about our family's work," which is a pretty honest approach.
Personal Details and Bio Data
Name | Joshua Jacobs |
Family Relation | Son of Jason Jacobs |
Involvement in Knife Business | Confirms family makes knives; speaks on past practices and current questions. |
Past Experience | Bought a "skinner" knife from his father's business when younger and less informed. |
Current Interests | Learning about custom knife pricing, especially fixed blades; seeking repair for an heirloom pocketknife. |
Early Days and the Jacobs Latter Pircing of Knowledge
Joshua remembers a time when he was much younger, and to be honest, he didn't know as much about knives as he does now. Back then, he actually bought one of his father's "skinner" knives. This personal experience is pretty telling, as it shows he was, in a way, just like many other customers, looking for a knife, but without a deep background in the subject. This sort of personal connection to the product, especially from someone who grew up around the business, really helps you see how things change over time, and how understanding grows, which is, you know, a common thing for all of us.
This period of his life, when he was "uneducated about knives," points to a sort of "Jacobs' latter pircing" of knowledge, if you will. It’s about the layers of understanding that develop over time. Just like a series of small, connected steps, his comprehension of the knife world has grown, moving from a basic customer perspective to someone now asking deeper questions about the trade. This personal growth is a big part of his story, showing that learning about any craft, especially one with a family legacy, is a continuous process. It's not something you just pick up all at once, you see.
His journey from being a less informed buyer to someone who now has specific questions about custom knife pricing shows a pretty significant shift. It’s a sign of his personal progression, of how his own "pircing" through the layers of the knife business has changed his perspective. This sort of personal history gives a lot of weight to what he says now, because he's seen things from different angles, both as a family member and as a consumer who, you know, just wanted a knife.
The Craft of Knifemaking - What's Really Going On?
The world of knifemaking is, as a matter of fact, pretty involved. It’s not just about shaping metal; it’s about a whole range of processes, from choosing the right materials to the skill of the person making the blade. There are different ways to approach it, too. Some makers start from scratch, forging their own steel, while others might work with pre-made blanks or components. Each method has its own set of challenges and, naturally, its own impact on the final product. Understanding these different approaches helps to clear up some of the mystery around what goes into a knife, and why some cost more than others, which is, you know, pretty helpful for anyone looking to buy.
The discussion around the Jacobs family business has touched on the idea of buying knives, then re-stamping and re-selling them. This practice, if it happens, would mean that the original maker's mark is removed and a new one put in its place. This kind of activity can raise questions about authenticity and the true origin of a knife, which is, obviously, a big deal for collectors and people who value craftsmanship. Joshua's statement about his family making knives seems to be a direct response to these kinds of concerns, aiming to clarify what their involvement truly is. It's about, basically, what's really happening behind the scenes.
The reason these discussions persist, for over a decade in this case, often comes down to transparency. People want to know where their products come from and who stands behind them. When there's a lack of clear information, or when practices are perceived as less than straightforward, questions tend to linger. Joshua's effort to speak out now, after all these years, suggests a desire to address these long-standing issues head-on, offering a clearer picture from someone directly connected to the family business. It’s a step towards, you know, being more open about things.
Is There a Jacobs Latter Pircing in the Knife Market?
When we talk about a "Jacobs' latter pircing" in the knife market, we might be thinking about the layers of value and how they are perceived, or perhaps, the way pricing unfolds over time for different types of knives. Is there a consistent pattern, a kind of layered structure, to how knives are priced, or how their value changes? This is a question that, you know, many buyers and sellers grapple with. It’s not always as simple as looking at the materials; there's much more to it than that, as a matter of fact.
Some might suggest that a "Jacobs' latter pircing" refers to the idea that some makers, like the Jacobs family, might have different levels or stages in their product offerings, or even in their business practices. For example, starting with more basic or acquired items, and then perhaps moving to more custom, in-house made pieces over time. This kind of progression, or the different tiers of a business, can affect how the market sees their products and what they are willing to pay. It’s about the different levels of engagement, if you will, that a company might have with its products, which is, you know, pretty common in many industries.
The question of whether there's a clear, observable "pircing" or layering in the market is really about how value is established and communicated. It involves looking at how brand reputation, material costs, labor, and even the story behind a knife all contribute to its final price. If there are different layers of quality or origin within a single brand, that can certainly affect buyer confidence and, basically, what people expect to pay. It's a pretty interesting point to consider when you're looking at the knife market as a whole, too it's almost.
What Goes Into Custom Knife Pricing, Anyway?
Joshua, as someone just starting to really look into this, has some questions about how custom knives, especially fixed blades, get their price tags. This is a very common question, because custom knife pricing can seem, you know, a bit mysterious from the outside. It's not just about the metal and the handle material. There are so many other factors that play a part, and it's something that, honestly, takes a lot of thought to really grasp.
For one thing, the knifemaker's time and skill are a huge part of the cost. Think about the hours spent designing the blade, shaping the steel, heat-treating it just right, and then grinding and polishing it to perfection. Each of these steps requires specialized knowledge and, basically, a steady hand. A maker's reputation also plays a role; a well-known artisan with a long waiting list can, naturally, charge more for their work. This is just like any other craft, where experience and a good name add value, you know.
Then there are the materials themselves. High-performance steels, exotic handle materials like rare woods or composites, and intricate embellishments can add significantly to the cost. The tools and equipment needed to create a custom knife are also a considerable investment for the maker. All these things add up, creating a price that reflects not just the physical components, but the artistry and dedication that went into making a unique piece. It’s a pretty complex calculation, really, that goes into each one.
Understanding Value - Beyond the Initial Purchase
When we talk about value, especially with items like custom knives, it's about much more than just the price you pay at the start. Value can be tied to the craftsmanship, the story behind the piece, or even its potential to become an heirloom. For something like a custom knife, the effort put into its creation, the quality of the materials, and the unique design all contribute to its long-term worth. It's not just a tool; it's, in a way, a piece of art or a personal statement, which is, you know, pretty significant.
Joshua brings up "Economics 101," which, basically, tells us that something is worth what someone is willing to pay for it. This simple idea holds true for knives, too. If a custom knife is highly sought after because of its maker's reputation or its unique features, its value can go up. On the other hand, if a knife is mass-produced with less attention to detail, its market value might be lower. It's about supply and demand, and also, the perceived quality and desirability of the item. This principle, you know, applies to almost everything we buy and sell.
The sentimental value of a knife, especially one that's been passed down through a family, adds another layer to its worth. This kind of value isn't measured in dollars, but in memories and connections. A knife might be old and worn, but if it belonged to a grandparent, its importance to the owner is immense. This is why people go to great lengths to repair and restore such items, even if the cost of repair might seem high compared to buying something new. It’s about preserving a piece of history, really, that means a lot to them.
Why Does a Jacobs Latter Pircing Matter for Heirloom Knives?
The idea of a "Jacobs' latter pircing" can be thought of as the layers of value and meaning that accumulate over time for an heirloom knife. An heirloom isn't just an old knife; it's a piece that has passed through generations, picking up stories and significance along the way. Each owner adds another layer to its history, making it, you know, more than just a tool. This progression of ownership and the memories attached to each stage contribute to its deep personal value, which is, honestly, quite unique.
For an heirloom like the Remington R1123 pocketknife Joshua is looking to restore, its "pircing" of value is quite distinct. It started as a manufactured item, but over time, it gained sentimental worth through its use and the hands it passed through. Its current "rough condition" is part of its story, too. The decision to repair it, rather than replace it, shows that its value isn't just about its market price, but about its history and the connection it provides to the past. It’s about preserving those layers, you know, that make it special.
This layered value means that when someone seeks to restore an heirloom, they are not just fixing a broken object. They are, basically, trying to preserve a piece of their family's narrative. The cost and effort involved in finding a skilled repair person reflect this deeper appreciation. It's a recognition that some things are worth more than their material components, and that their true value lies in their journey through time and the personal meaning they hold. This is why, you know, these old items are so cherished.
Finding the Right Hands - Repairing a Piece of History
When you have something truly special, like an heirloom knife that has seen better days, finding the right person to fix it is, as a matter of fact, a really big deal. It's not just any repair job; it requires someone with a particular set of skills and a deep respect for the item's history. An old Remington R1123 pocketknife, especially one that's "pretty valuable" but in "fairly rough condition," needs someone who understands its construction, its materials, and how to bring it back to life without erasing its past. This search for the perfect craftsperson is, you know, a journey in itself.
Joshua is specifically looking for an Oregon knifemaker to take on this task. This geographical preference might be for practical reasons, like being able to meet the maker in person, or it could be because he knows of a strong community of skilled artisans in that area. Finding a local expert can sometimes make the process much smoother, allowing for direct communication and a better understanding of what the restoration will involve. It’s about finding someone you can trust with something so meaningful, which is, basically, a key part of the whole process.
The challenge with repairing vintage items is that parts might be hard to find, and the techniques used to make them originally might be different from modern methods. A good restorer needs to be able to work with these older materials and techniques, ensuring that the repair is not only functional but also sympathetic to the knife's original character. It's a delicate balance between making it usable again and preserving its historical integrity. This kind of work is, you know, really an art form in itself, requiring a lot of patience and skill.
Where Can You Find a Skilled Jacobs Latter Pircing Specialist?
So, if you're looking for someone who can handle the "Jacobs' latter pircing" of an heirloom knife – that is, someone who can restore the layers of its history and value – where do you even begin to look? It’s not like you can just type "heirloom knife repair" into a search bar and find the perfect person right away. This kind of specialized skill requires a bit more digging, and often, relies on personal recommendations or connections within the craft community. It’s about finding someone who really gets it, you know, and can handle something so important.
One good place to start is by reaching out to local knifemaking guilds or associations. These groups often have members who specialize in different aspects of the craft, including restoration. Attending knife shows or online forums dedicated to custom knives and vintage blades can also connect you with experienced makers and restorers. Sometimes, the best specialists are found through word of mouth, as people who have had positive experiences with a restorer are usually very happy to share their recommendations. It’s about tapping into that network, basically, to find the right person.
A "Jacobs' latter pircing" specialist, in this context, is someone who understands the nuanced value of an old knife, beyond its material worth. They recognize that each scratch, each bit of wear, tells a part of its story. Their work isn't just about fixing; it's about honoring that history while making the knife usable and stable for future generations. It’s a very particular kind of expertise, and finding someone with that level of care and skill is, you know, truly a treasure. This kind of work is really about preserving history, one layer at a time.
This article has aimed to shed some light on the ongoing conversation around the Jacobs family and their knife business, particularly from Joshua Jacobs' perspective. We've talked about his family's long-standing connection to knifemaking, the discussions around how knives are acquired and sold, and Joshua's personal journey of learning about the craft. We also looked at the many things that go into pricing custom knives, how value changes over time, and the special care needed for treasured heirloom pieces like the Remington R1123 pocketknife Joshua hopes to restore. It’s all about understanding the different layers and stories within the world of knives.
Additional Resources
Visual Content
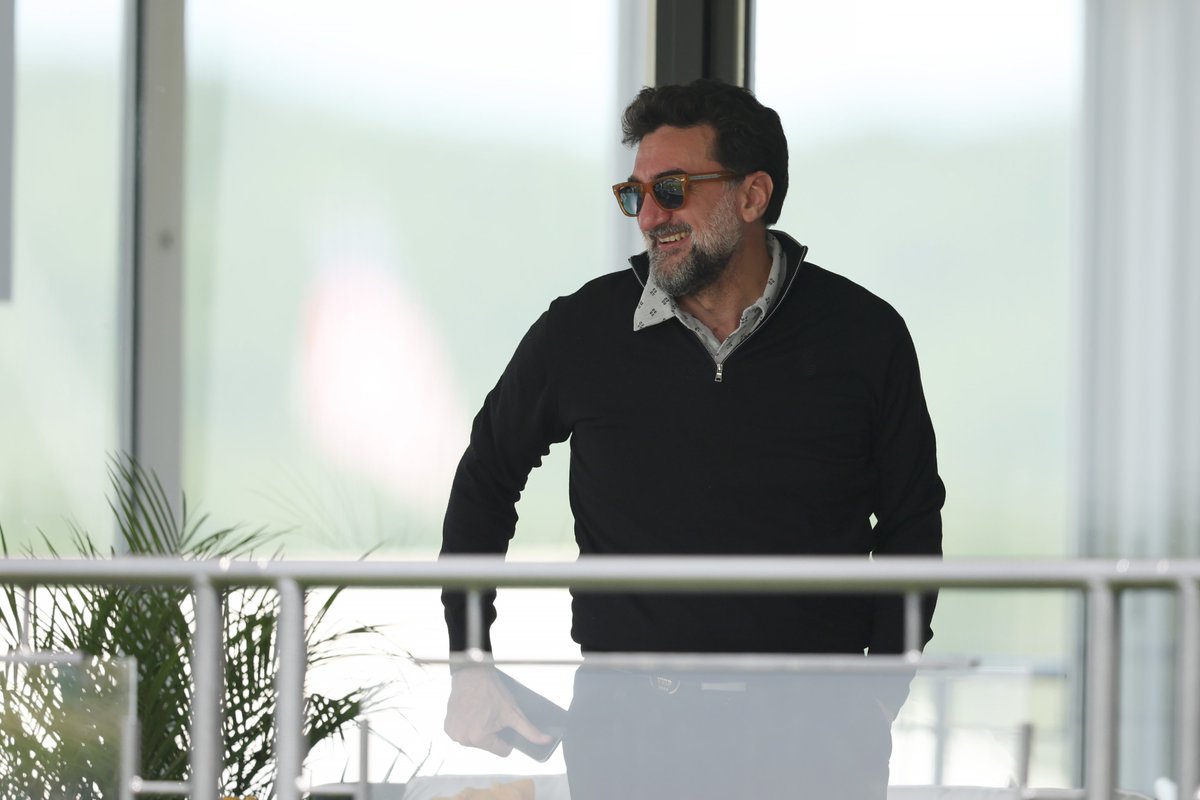

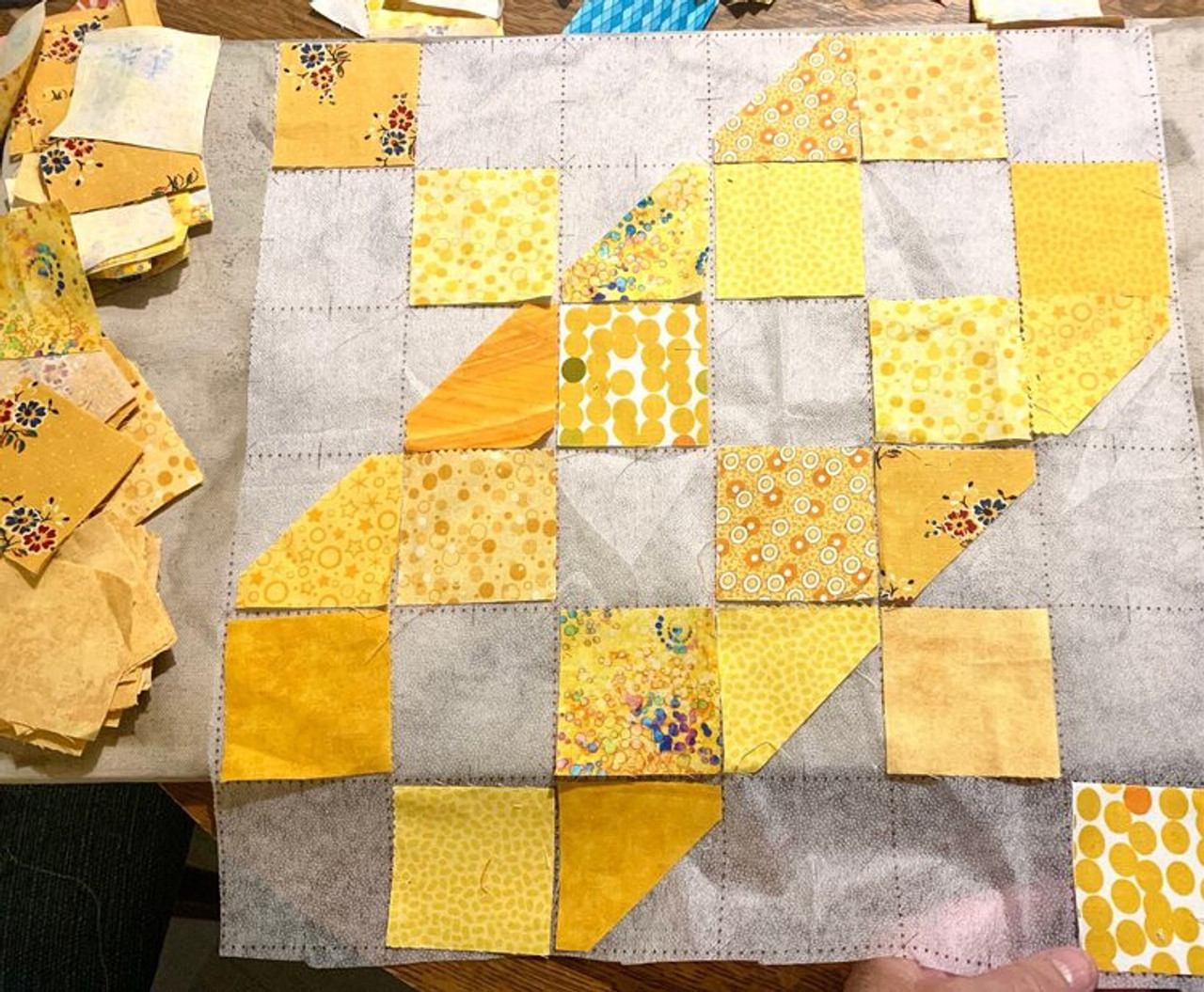
Disclaimer: This content was generated using AI technology. While every effort has been made to ensure accuracy, we recommend consulting multiple sources for critical decisions or research purposes.